MATTRIS’25 by A3TS : une édition record sous le signe de l'innovation et des enjeux énergétiques du futur
Organisé du 2 au 4 juillet au Parc des Expositions et des Congrès de Dijon, le Congrès-Salon Mattris ‘25 by A3TS a confirmé son statut d’événement de référence dans le domaine des traitements thermiques et de l’ingénierie des surfaces.
Plus de 1000 participants issus d'entreprises, de centres technologiques et de laboratoires de recherche d'une quinzaine de pays se sont retrouvés pour échanger autour des dernières innovations dans le traitement des matériaux métalliques. Un public nombreux d’étudiants et de jeunes diplômés fut également présent.
Au programme :
75 conférences de haut niveau en français et en anglais sous titrées, animées par des experts venus des quatre coins du globe.
250 congressistes, nationaux et internationaux
80 exposants, industriels, centres de recherche, universités
600 visiteurs qualifiés ont convergé à Dijon.
Le salon a également accueilli de nombreuses initiatives fédératrices :
deux tables rondes d’experts, l’une sur le thème de l’Économie circulaire & recyclabilité des matériaux : quels enjeux pour les traitements thermiques et de surface ?, l’autre sur les Enjeux Matériaux pour les Energies du futur.
des rendez-vous BtoB ciblés,
le concours de l’Innovation A3TS,
le concours photo sur le thème des traitements des matériaux sous l’oeil du microscope,
la remise des Trophées Jeunes UITS,
la remise des Prix de thèse en Traitement thermique et en Traitement de surface,
le job dating.
Un programme de visites de sites emblématiques de la région a été proposé :
les sites de Framatome de Saint-Marcel et de Montbard,
le site des Forges de Courcelles à Nogent,
la plateforme de l’UTT à Nogent,
la plateforme Calhipso à Dijon,
les sites d’Amphenol FCI et d’Aalberts de Besançon,
Smart Energy, station de fabrication et de distribution d’hydrogène à Dijon.
Les conférences plénières
Une vision des matériaux et de la fabrication du nucléaire de demain
Jean DHERS, Head of Materials - NEWCLEO
Innovative and sustainable steels for nuclear application
Nathalie PAUZE, Nuclear Head of Sales - INDUSTEEL
Traitements haute température en métallurgie des poudres (procédé MIM). Objectifs et écarts par rapport aux traitements thermiques traditionnels. Modélisation et conséquences sur la chimie.
Jean Claude BIHR, PDG - Docteur en métallurgie et industrie française - ALLIANCE MIM
Alloys electrodeposition: the basis, the trends, the future
Jean-Yves HIHN, Head of Sonochemistry and Surface Reactivity Group - Université Marie et Louis Pasteur, CNRS UTINAM
À la rencontre des exposants du Salon MATTRIS 2025
Organisé en parallèle des conférences, le Salon MATTRIS 2025 a réuni 80 exposants venus présenter leurs innovations, équipements et savoir-faire. Cet espace d’exposition a favorisé le réseautage, la découverte de solutions technologiques de pointe et l’émergence de collaborations autour des domaines suivants :
Fours et équipements pour le traitement thermique
Traitement et revêtement des surfaces
Mesure, contrôle et régulation
Procédés et services en traitement thermique et traitement de surface
Spécialités chimiques et consommables
Études, R&D, ingénierie et conseil
Un temps fort pour les professionnels du secteur, marqué par la richesse des échanges et la qualité des contacts établis.
Table ronde : Économie circulaire & recyclabilité des matériaux : quels enjeux pour les traitements thermiques et de surface ?
Le 2 juillet, sur la salon, une table ronde inédite a réuni 4 intervenants issus de différents maillons de la chaîne de valeur pour échanger sur un enjeu de plus en plus stratégique : 𝐥𝐞𝐬 𝐜𝐨𝐧𝐬𝐞́𝐪𝐮𝐞𝐧𝐜𝐞𝐬 𝐜𝐨𝐧𝐜𝐫𝐞̀𝐭𝐞𝐬 𝐝𝐞𝐬 𝐩𝐨𝐥𝐢𝐭𝐢𝐪𝐮𝐞𝐬 𝐝’𝐞́𝐜𝐨𝐧𝐨𝐦𝐢𝐞 𝐜𝐢𝐫𝐜𝐮𝐥𝐚𝐢𝐫𝐞 𝐬𝐮𝐫 𝐥𝐞𝐬 𝐟𝐢𝐥𝐢𝐞̀𝐫𝐞𝐬 𝐢𝐧𝐝𝐮𝐬𝐭𝐫𝐢𝐞𝐥𝐥𝐞𝐬 𝐭𝐫𝐚𝐢𝐭𝐚𝐧𝐭 𝐝𝐞𝐬 𝐦𝐚𝐭𝐞́𝐫𝐢𝐚𝐮𝐱.
🎙 Animée par Etienne Bouyer - CEA (Direction des Programmes), parole a été donnée à :
💬 Les échanges ont d’abord porté sur les𝐩𝐫𝐢𝐧𝐜𝐢𝐩𝐚𝐮𝐱 𝐦𝐨𝐭𝐞𝐮𝐫𝐬 𝐝𝐞 𝐥’𝐞́𝐜𝐨𝐧𝐨𝐦𝐢𝐞 𝐜𝐢𝐫𝐜𝐮𝐥𝐚𝐢𝐫𝐞 : 𝐩𝐫𝐞𝐬𝐬𝐢𝐨𝐧 𝐫𝐞́𝐠𝐥𝐞𝐦𝐞𝐧𝐭𝐚𝐢𝐫𝐞, 𝐬𝐨𝐮𝐯𝐞𝐫𝐚𝐢𝐧𝐞𝐭𝐞́ 𝐬𝐭𝐫𝐚𝐭𝐞́𝐠𝐢𝐪𝐮𝐞, 𝐚𝐭𝐭𝐞𝐧𝐭𝐞𝐬 𝐑𝐒𝐄 𝐝𝐞𝐬 𝐝𝐨𝐧𝐧𝐞𝐮𝐫𝐬 𝐝’𝐨𝐫𝐝𝐫𝐞... Des dynamiques influençant directement fournisseurs et sous-traitants.
🔹 𝐐𝐮𝐚𝐧𝐭𝐢𝐭𝐞́ : l’Europe 𝐦𝐚𝐧𝐪𝐮𝐞 𝐝𝐞 𝐦𝐚𝐭𝐞́𝐫𝐢𝐚𝐮𝐱 𝐫𝐞𝐜𝐲𝐜𝐥𝐞́𝐬. De nombreux véhicules, avions ou ferrailles quittent le continent en fin de vie, privant les filières locales de ressources clés pour réduire leur dépendance aux métaux neufs. Cette rareté 𝐜𝐨𝐦𝐩𝐥𝐢𝐪𝐮𝐞 𝐥𝐚 𝐦𝐨𝐧𝐭𝐞́𝐞 𝐞𝐧 𝐩𝐮𝐢𝐬𝐬𝐚𝐧𝐜𝐞 𝐝𝐞𝐬 𝐩𝐫𝐨𝐜𝐞́𝐝𝐞́𝐬 comme la seconde fusion électrique.
🔹 𝐐𝐮𝐚𝐥𝐢𝐭𝐞́ : les métaux recyclés présentent des 𝐜𝐨𝐦𝐩𝐨𝐬𝐢𝐭𝐢𝐨𝐧𝐬 𝐯𝐚𝐫𝐢𝐚𝐛𝐥𝐞𝐬, nécessitant 𝐭𝐫𝐢 𝐫𝐢𝐠𝐨𝐮𝐫𝐞𝐮𝐱 𝐞𝐭 𝐚𝐝𝐚𝐩𝐭𝐚𝐭𝐢𝐨𝐧 𝐝𝐞𝐬 𝐩𝐫𝐨𝐜𝐞́𝐝𝐞́𝐬. Ces défis peuvent devenir des opportunités, en intégrant l’économie circulaire dès la conception des pièces.
🔧 𝐀𝐮𝐭𝐫𝐞𝐬 𝐥𝐞𝐯𝐢𝐞𝐫𝐬 𝐞́𝐯𝐨𝐪𝐮𝐞́𝐬 : 𝐫𝐞́𝐩𝐚𝐫𝐚𝐛𝐢𝐥𝐢𝐭𝐞́, 𝐚𝐥𝐥𝐨𝐧𝐠𝐞𝐦𝐞𝐧𝐭 𝐝𝐞 𝐥𝐚 𝐝𝐮𝐫𝐞́𝐞 𝐝𝐞 𝐯𝐢𝐞, 𝐜𝐨𝐧𝐜𝐞𝐩𝐭𝐢𝐨𝐧 𝐩𝐨𝐮𝐫 𝐥𝐞 𝐝𝐞́𝐦𝐨𝐧𝐭𝐚𝐠𝐞, 𝐫𝐞𝐭𝐫𝐨𝐟𝐢𝐭 𝐝𝐞𝐬 𝐞́𝐪𝐮𝐢𝐩𝐞𝐦𝐞𝐧𝐭𝐬… Par exemple, le rétrofit de fours industriels permettrait de réduire de 50 % l’utilisation de métal neuf pour une nouvelle installation.
💡 En conclusion, les intervenants ont rappelé que 𝐥’𝐞́𝐜𝐨𝐧𝐨𝐦𝐢𝐞 𝐜𝐢𝐫𝐜𝐮𝐥𝐚𝐢𝐫𝐞 𝐧𝐞 𝐩𝐞𝐮𝐭 𝐞̂𝐭𝐫𝐞 𝐝𝐢𝐬𝐬𝐨𝐜𝐢𝐞́𝐞 𝐝𝐞 𝐬𝐞𝐬 𝐫𝐞́𝐚𝐥𝐢𝐭𝐞́𝐬 𝐞́𝐜𝐨𝐧𝐨𝐦𝐢𝐪𝐮𝐞𝐬. Son succès repose sur une 𝐜𝐨𝐨𝐫𝐝𝐢𝐧𝐚𝐭𝐢𝐨𝐧 𝐝𝐞 𝐥’𝐞𝐧𝐬𝐞𝐦𝐛𝐥𝐞 𝐝𝐞 𝐥𝐚 𝐜𝐡𝐚𝐢̂𝐧𝐞 – producteurs, transformateurs, recycleurs – dans un 𝐜𝐚𝐝𝐫𝐞 𝐫𝐞́𝐠𝐥𝐞𝐦𝐞𝐧𝐭𝐚𝐢𝐫𝐞 𝐚𝐝𝐚𝐩𝐭𝐞́ 𝐞𝐭 𝐜𝐨𝐡𝐞́𝐫𝐞𝐧𝐭.
🎥 La vidéo de cette table ronde sera bientôt disponible sur notre site
Table ronde "Enjeux Matériaux pour les Énergies du Futur”
🔋 𝐒𝐚𝐧𝐬 𝐦𝐚𝐭𝐞́𝐫𝐢𝐚𝐮𝐱 𝐚𝐝𝐚𝐩𝐭𝐞́𝐬, 𝐩𝐚𝐬 𝐝𝐞 𝐭𝐫𝐚𝐧𝐬𝐢𝐭𝐢𝐨𝐧 𝐞́𝐧𝐞𝐫𝐠𝐞́𝐭𝐢𝐪𝐮𝐞 𝐯𝐢𝐚𝐛𝐥𝐞.
C’est le constat partagé par les intervenants de la table ronde du 3 juillet, organisée dans le cadre de MATTRIS '25 by A3TS.
Qu’il s’agisse de produire de l’énergie décarbonée, de la transporter ou de mieux la consommer, les matériaux et leurs traitements sont au cœur de tous les défis techniques et économiques à relever.
🎙 Animée par Pierre BRUCHET, elle réunissait :
Hanlin Liao – Professeur à l’Université de Technologie de Belfort-Montbéliard
Daniel Lincot – Directeur de recherche émérite CNRS, fondateur de SOYPV
Jorge Arturo Soto Puente – Ingénieur recherche, Cetim - Centre technique des industries mécaniques
🌞 𝐏𝐡𝐨𝐭𝐨𝐯𝐨𝐥𝐭𝐚𝐢̈𝐪𝐮𝐞 – Daniel LINCOT a souligné l’importance stratégique de cette filière, aujourd’hui dominée par l’Asie. Pour que l’Europe reprenne la main, il faut 𝐚𝐦𝐞́𝐥𝐢𝐨𝐫𝐞𝐫 𝐥𝐞𝐬 𝐫𝐞𝐧𝐝𝐞𝐦𝐞𝐧𝐭𝐬 𝐞𝐭 𝐫𝐞́𝐝𝐮𝐢𝐫𝐞 𝐥𝐞𝐬 𝐜𝐨𝐮̂𝐭𝐬 𝐝𝐞 𝐩𝐫𝐨𝐝𝐮𝐜𝐭𝐢𝐨𝐧, en s’appuyant sur des 𝐭𝐫𝐚𝐢𝐭𝐞𝐦𝐞𝐧𝐭𝐬 𝐝𝐞 𝐬𝐮𝐫𝐟𝐚𝐜𝐞 𝐚𝐯𝐚𝐧𝐜𝐞́𝐬. Une stratégie industrielle volontariste et des centres de compétence sont indispensables pour bâtir une filière souveraine.
💧 𝐇𝐲𝐝𝐫𝐨𝐠𝐞̀𝐧𝐞 – Hanlin LIAO a rappelé les 𝐧𝐨𝐦𝐛𝐫𝐞𝐮𝐱 𝐝𝐞́𝐟𝐢𝐬 posés par ce 𝐠𝐚𝐳 𝐢𝐧𝐬𝐭𝐚𝐛𝐥𝐞 𝐞𝐭 𝐝𝐢𝐟𝐟𝐢𝐜𝐢𝐥𝐞 𝐚̀ 𝐦𝐚𝐢̂𝐭𝐫𝐢𝐬𝐞𝐫. Dans les 𝐞́𝐥𝐞𝐜𝐭𝐫𝐨𝐥𝐲𝐬𝐞𝐮𝐫𝐬, les électrodes sont un maillon critique : des 𝐦𝐚𝐭𝐞́𝐫𝐢𝐚𝐮𝐱 𝐢𝐧𝐧𝐨𝐯𝐚𝐧𝐭𝐬, associés à des procédés comme la 𝐩𝐫𝐨𝐣𝐞𝐜𝐭𝐢𝐨𝐧 𝐭𝐡𝐞𝐫𝐦𝐢𝐪𝐮𝐞 ou l’𝐞́𝐥𝐞𝐜𝐭𝐫𝐨𝐝𝐞́𝐩𝐨𝐬𝐢𝐭𝐢𝐨𝐧, permettent de viser 𝐩𝐞𝐫𝐟𝐨𝐫𝐦𝐚𝐧𝐜𝐞, 𝐝𝐮𝐫𝐚𝐛𝐢𝐥𝐢𝐭𝐞́ 𝐞𝐭 𝐛𝐚𝐢𝐬𝐬𝐞 𝐝𝐞𝐬 𝐜𝐨𝐮̂𝐭𝐬.
🔬 𝐓𝐫𝐚𝐢𝐭𝐞𝐦𝐞𝐧𝐭𝐬 𝐝𝐞 𝐬𝐮𝐫𝐟𝐚𝐜𝐞 – Arturo SOTO a détaillé les exigences imposées par l’hydrogène sur les composants : 𝐞́𝐭𝐚𝐧𝐜𝐡𝐞́𝐢𝐭𝐞́, 𝐫𝐞́𝐬𝐢𝐬𝐭𝐚𝐧𝐜𝐞 𝐚̀ 𝐥𝐚 𝐟𝐫𝐚𝐠𝐢𝐥𝐢𝐬𝐚𝐭𝐢𝐨𝐧, 𝐜𝐨𝐦𝐩𝐚𝐭𝐢𝐛𝐢𝐥𝐢𝐭𝐞́ 𝐜𝐡𝐢𝐦𝐢𝐪𝐮𝐞. Les traitements de surface sont la clé de la sécurité et de la pérennité de la filière H₂.
⚙️ 𝐒𝐨𝐛𝐫𝐢𝐞́𝐭𝐞́ 𝐞́𝐧𝐞𝐫𝐠𝐞́𝐭𝐢𝐪𝐮𝐞 – Bruno CAUWE a rappelé deux leviers puissants mais souvent négligés : la 𝐫𝐞́𝐝𝐮𝐜𝐭𝐢𝐨𝐧 𝐝𝐞𝐬 𝐟𝐫𝐨𝐭𝐭𝐞𝐦𝐞𝐧𝐭𝐬 et l’𝐨𝐩𝐭𝐢𝐦𝐢𝐬𝐚𝐭𝐢𝐨𝐧 𝐝𝐢𝐦𝐞𝐧𝐬𝐢𝐨𝐧𝐧𝐞𝐥𝐥𝐞 𝐝𝐞𝐬 𝐬𝐲𝐬𝐭𝐞̀𝐦𝐞𝐬, pour limiter les pertes d’énergie dès la conception.
💡 Cette table ronde l’a confirmé : les matériaux ne sont pas une simple ressource, ils sont un levier stratégique pour réussir la transition énergétique.
Le Prix de l'innovation A3TS 2025 décerné à AML Innovation pour le LiCS Coating®
AML Innovation est une entreprise du groupe AML situé au nord de Metz dédiée à l’innovation de rupture sur les traitements de surface innovants et le brasage sous vide multi-matériaux pour les marchés de la défense, de l'aéronautique, du spatial. L'entreprise a été créée en 2021 et a bénéficié du soutien du Plan de Relance de l’État pour l'invention et le développement d’une technologie disruptive appelée LiCS Coating® (Liquid Chemical Suspension Coating), destinée aux dépôts métalliques sur des pièces usinées et/ou imprimées en 3D.
LiCS Coating® est une nouvelle technologie de revêtement et de fonctionnalisation de surface basée sur l’utilisation d’une suspension liquide contenant de la poudre de métaux/alliages métalliques. Ce revêtement s'adapte bien à toutes formes, tailles et types de substrats métalliques/céramiques et a été conçu pour être appliqué sur des canaux internes de morphologies complexes, ou en externe, de manière sélective ou non. Cette technologie est REACh-compatible et n’utilise pas de bains chimiques.
-
LiCS Coating® est une nouvelle technologie de revêtement et de fonctionnalisation de surface basée sur l’utilisation d’une suspension liquide contenant de la poudre de métaux/alliages métalliques. Ce revêtement s'adapte bien à toutes formes, tailles et types de substrats métalliques/céramiques (usinés, obtenus par FabAdd…) et a été conçu pour être appliqué sur des canaux internes de morphologies complexes, ou en externe, de manière sélective ou non. Cette technologie est REACh-compatible et n’utilise pas de bains.
Question 1 : Dans quel(s) contexte(s) l'innovation est-elle envisagée ?
La technologie LiCS Coating® a été initialement développée pour résoudre un problème spécifique dans l'industrie aéronautique. Pour connecter des émetteurs et récepteurs micro-ondes à leurs antennes, dans des équipements tels que les radars, les communications par satellite et les liaisons radio microondes, des guides d’ondes sont utilisées pour véhiculer les ondes entre les différentes fonctions. Il s’agit généralement d’un tube métallique creux dont la surface intérieure doit être conductrice. Les guides d'ondes sont généralement fabriqués à partir de matériaux comme l’aluminium, le cuivre, l’inox ou le titane, avec les surfaces internes plaquées électro-chimiquement de cuivre, d'argent ou d'or. Cependant, avec l’augmentation des fréquences, les canaux des guides d’ondes ont rétréci jusqu’à ce que les méthodes de revêtement traditionnelles soient devenues très difficiles à utiliser, voir inapplicables. Il est donc apparu nécessaire de développer une technologie pour fonctionnaliser des canaux internes formes complexes, ce qui a abouti à la création et à la mise en œuvre du LICS Coating®.
Question 2 : Quel est le niveau de maturité atteint par l'innovation ? Quelles sont les références industrielles ?
AML Innovation dispose actuellement d'une ligne de production de pièces métalliques traitées avec la technologie de revêtement LiCS Coating ®. Depuis 2022, les pièces sont livrées à notre client évoluant sur le marché de la défense et de l’aéronautique à une fréquence d'environ une à deux lignes par mois.
Question 3 : Expliquez comment l'innovation peut contribuer à la performance industrielle de son utilisateur. Sur quels critères peut-on mesurer son impact ?
Le LiCS Coating ® peut aussi bien être appliqué sur des surfaces lisses usinées, que des surfaces rugueuses comme la fonderie ou l’impression 3DLe procédé a été créé pour atteindre des surfaces ou fonctionnaliser des canaux que les technologies actuelles ne permettent pas d’atteindre.Le procédé combine une étape d’application d’une suspension liquide à base du ou des alliages que l’on souhaite déposer, et un traitement thermique qui va faire fondre ladite suspension pour réaliser la liaison entre le substrat et le revêtement. Nous n’utilisons pas de bains chimiques pour réaliser nos traitementsAinsi plusieurs opérations peuvent être réalisées en même temps (sous conditions) :
La fonctionnalisation de surface
Le lissage des surfaces
L’amélioration des caractéristiques mécaniques (tenue en fatigue)
Le piégeage des particules détachables dans le revêtement
Une tenue mécanique et thermique du revêtement très élevée
La pénétration du substrat pour en boucher les porosités ou fissures
Le brasage
Et le traitement thermique
Nous pensons donc que le LiCS Coating® contribue à la performance industrielle en mutualisant certaines opérations et ainsi en reconsidérant les schémas industriels classiques. Il faut aussi considérer que le LiCS Coating® propose une véritable rupture de technologie notamment dans le monde de la 3D permettant ainsi de repousser les limites les pièces et produits réalisés en fabrication additive. L’impact peut ainsi être mesuré en termes de coût, de solutions alternatives, d’impact écologique, ou tout simplement de faisabilité.
Question 4 : Expliquez le contenu technologique de l'innovation. Quels étaient les défis techniques à relever ? Quelles sont les solutions / technologies concurrentes ?
La technologie LiCS Coating® est une méthode innovante de revêtement et/ou de fonctionnalisation de surface basée sur l'utilisation d'une suspension. Généralement, la suspension contient de la poudre métallique (métal pur ou alliages) et un liant liquide. La composition de la suspension peut être modifiée et adaptée à un besoin spécifique, ce qui constitue l'un des principaux avantages de l'invention. Un autre avantage est que, grâce à sa forme liquide, cette innovation est adaptée aux pièces en métal/céramique de toute géométrie, avec cavités internes simples ou complexes, pour un revêtement de surface complet ou sélectif.
Et enfin, le LiCS Coating® présente une gamme assez simple et intrinsèquement écoresponsable, comparé aux autres procédés. Des solutions/technologies telles que le dépôt en phase vapeur, la galvanisation, le dépôt chimique humide, les revêtements de conversion (pulvérisation ou trempage), la projection thermique peuvent être considérées comme des technologies concurrentes.
La présente invention revendique une rupture technologique vis-à-vis de ces solutions et notamment grâce aux points suivants :
La qualité du revêtement (homogène, régulier et non poreux);
L'épaisseur du revêtement réglable et homogène ;
La dimension des canaux revêtus (actuellement 0,8mm de diamètre)
La tenue mécanique et thermique du revêtement ; la surface est ré-usinable (par exemple, polissage mécanique ou usinage) ;
Donne une fonction à la surface (cosmétique ou technique : conductrice, augmentation de la dureté de surface, protection anti-corrosion…) ;
La solution est adaptée aux pièces de toutes géométries, possédant ou non des cavités internes simples ou complexes, dans le cadre d’un recouvrement des surfaces complet ou sélectif.
Question 5 : L'innovation contribue-t-elle à améliorer l'impact environnemental de l'utilisateur industriel ?
L’innovation présentée est un procédé éco-responsable et conforme aux exigences REACh. De plus, d’autres indicateurs importants du respect de l’environnement du procédé peuvent être ajoutés :
Utilisation de la juste quantité de suspension vs surface à couvrir ;
Pas de chimie, comparé aux procédés de dépôt chimique ou électrolytique ;
Peu de rejets ;
Pas de déchets chimiques à retraiter ;
Pas de bain à maintenir – pas de chimie hors préparation de surface si nécessaire ;
Certains types de poudres utilisées pour l’innovation peuvent être collectées, recyclées et réutilisées.
Contact : Jean-Yves MILOJEVIC et Daria Zhemchuzhnikova PhD
jeanyves.milojevic@aml-microtec.com
daria.zhemchuzhnikova@aml-microtec.com
Quatre autres innovations concouraient pour ce prix :
-
L'analyseur de gaz intelligent intégré à la plateforme Smart Technologies d'Air Products est conçu de manière modulaire. Les composants nécessaires à la surveillance et au contrôle d'un procédé de traitement thermique spécifique sont sélectionnés et configurés en conséquence. L'analyseur intelligent lui-même comprend jusqu'à 7 capteurs d'atmosphère sélectionnables, un ensemble de logiciels requis pour le processus spécifique, l'acquisition de données de processus et le téléchargement vers la plateforme basée sur le cloud pour la visualisation, la documentation et l'extraction de données. L'acquisition des données est extensible pour inclure les données sur les matériaux et la qualité et peut être reliée à un réseau de données client tel qu'un système Scada ou un PLC pour fournir une récupération de données étendue telle que l'identification des tendances et des corrélations de processus qui aident à analyser et à fournir un retour d'information pour améliorer le processus.
Question 1 : Dans quel(s) contexte(s) l'innovation est-elle envisagée ?
L'objectif principal de l'innovation est d'apporter au client une plus grande efficacité dans l'utilisation des ressources afin de produire peu ou pas de déchets, d'améliorer la productivité avec peu ou pas de retouches, de réduire les coûts de production et donc de réduire l'empreinte carbone de la production.
Question 2 : Quel est le niveau de maturité atteint par l'innovation ? Quelles sontles références industrielles ?
La solution est actuellement installée sur trois sites de clients en Allemagne, dont un dans le cadre d'un consortium parrainé par le gouvernement allemand, le projet HydroConnect.
Question 3 : Expliquez comment l'innovation peut contribuer à la performanceindustrielle de son utilisateur. Sur quels critères peut-on mesurer son impact ?
L'analyseur de gaz intelligent et les services Smart Technologies d'Air Products permettent d'optimiser les processus de traitement thermique, les options de contrôle des processus et la surveillance locale, tandis que les données collectées dans le cloud peuvent être utilisées pour examiner les écarts de processus, identifier les liens entre les valeurs de processus, évaluer la qualité des pièces et permettre des réglages de processus optimaux plutôt que de suivre des paramètres fixes et une approche empirique dans l'exécution du processus.
L'acquisition de données est extensible pour inclure les données relatives aux matériaux et à la qualité et peut être reliée à un réseau de données client tel qu'un système Scada ou un automate programmable afin de fournir une extraction de données étendue telle que l'identification des tendances et des corrélations de processus qui aident à analyser et à fournir un retour d'information pour améliorer le processus.
Question 4 : Expliquez le contenu technologique de l'innovation. Quels étaient les défis techniques à relever ? Quelles sont les solutions / technologies concurrentes ?
La surveillance et le contrôle du processus de traitement thermique, ainsi que l'acquisition et la documentation des données, sont connus de l'industrie et largement couverts par le système. L'innovation réside dans la réception des données et le retour des résultats analytiques au processus, ce qui implique la mise en œuvre d'algorithmes d'apprentissage automatique, la fourniture d'informations consultatives pour améliorer le processus et la prévision de la qualité, la productivité tels que le chargement des fours, le droit à la maintenance préventive.
Question 5 : L'innovation contribue-t-elle à améliorer l'impact environnemental de l'utilisateur industriel ?
Cette solution présente des avantages pour le client, car elle assure la transparence, la traçabilité et la documentation du processus, ce qui permet de l'optimiser.
Les principaux avantages pour le client sont une plus grande efficacité dans l'utilisation des ressources, car peu ou pas de déchets sont produits, une productivité accrue, car peu ou pas de retouches, une réduction des coûts de production et donc une réduction de l'empreinte carbone de la production.
-
Cellule de nitruration, carbonitruration, modulaire à parois froide, avec élément chauffant métallique (Suppression du risque HCN), pression d'utilisation de vide primaire à la PA, Installation qui est en cours de fabrication, et sera installé sur nos centre d'essai de Grenoble et des USA. Cette nouvelle cellule vient compléter la versatilité de notre ICBP, et est disponible en taille 966, 1T, ou 1299, 2T.
Question 1 : Dans quel(s) contexte(s) l'innovation est-elle envisagée ?
Cette innovation née du besoin industriel de pouvoir maitriser les phases de carbonitruration à basse pression, à des fins de réduction de consommations d'utilités, et d'émission de CO2. L'idée est de faire les phases de cémentation à haute température 940-980 dans une cellule, et transférer dans une cellule à plus basse température pour faire la phase de carbonitruration.
Question 2 : Quel est le niveau de maturité atteint par l'innovation ? Quelles sont les références industrielles ?
Le système central, qu'est l'ICBP, est lui maitrisé, et déployé mondialement depuis plus de 30 ans. Deux limitations existent en faisant les deux phases enchaînées à même température: 1) Le NH3 se recombine trop rapidement à haute température, d'où une mauvaise homogénéité process. 2) La génération de HCN par contact du NH3 avec les éléments graphites. Le premier point a été soldé par des essais avec des clients industrielles automobiles (Européens, et chinois), ie. faire les phases de cémentation, et carbonitruration dans différentes chambres à différentes températures, avec un transfert sous vide. La problématique restante à solder étant la génération HCN. La nouvelle cellule est réalisée avec des éléments chauffants métalliques. Elle a été brevetée et est en cours de fabrication, et sera installée sur nos centres d'essais de Grenoble et des USA d'ici la fin de l'année.
Question 3 : Expliquez comment l'innovation peut contribuer à la performance industrielle de son utilisateur. Sur quels critères peut-on mesurer son impact ?
Elle supprime le risque HCN de part sa conception sans élément graphite.
Son coût de fabrication est diminuée du fait d'avoir un four à parois froides et non un four moufflet.
Enfin nous allons retrouver toutes les avantages économiques d'une installation modulaire : consommation réduite via le refroidissement en chambre séparée, mais aussi via le fait de pouvoir jouer avec une pression de traitement allant du vide primaire à la PA (suite à une purge par le vide)
Question 4 : Expliquez le contenu technologique de l'innovation. Quels étaient les défis techniques à relever ? Quelles sont les solutions / technologies concurrentes ?
Cellule multi procédés permettant de faire de la nitruration avec post-ox, et des phase de carbonitruration. De facto, une cellule pouvant travailler avec précision +/-5°C de 400°C à 900°C, et ceux du vide primaire jusqu'à la PA, intégrant les utilités process suivants : NH3,N20,CO2,Air,Eau
Aujourd'hui notre concurrence en four multi chambre n'a pas, à notre connaissance, proposé de solution. Les conclusions d'ALD (cf. conférence A3TS à Toulouse) sont les mêmes que les notre lorsque l'on fait toutes les phases dans un même four graphite : homogénéité de traitement sur 1/4 de la charge, et génération de HCN
Question 5 : L'innovation contribue-t-elle à améliorer l'impact environnemental de l'utilisateur industriel ?
Cette innovation a pour but de supprimer à termes les fours atmosphériques à gaz de carbonitruration, et donc par conséquent grandement réduire les émissions de CO2
-
Is it possible to save up to 80% gas and achieve better results at the same time? -YES, IT IS – with Ipsen GreenFlow.
The intelligent system dynamically reduces gas supply in real time – adapted to your processes and production conditions.
After loading, GreenFlow precisely measures the furnace atmosphere – and automatically adjusts the gas supply. The system reacts in real time to door movements or atmospheric changes and keeps the protective gas atmosphere constant – more efficiently than any conventional control system.
Question 1 : Dans quel(s) contexte(s) l'innovation est-elle envisagée ?
Increasing the energy efficiency of heat treatment: The aim of the GreenFlow gasification system is to save process media and heating energy in order to make atmospheric carburising and (case) hardening processes as energy-efficient as possible. Due to the high savings in process media and heating energy (regardless of whether this is achieved through gas burners or electric heating), CO2 emissions are also drastically reduced.
Question 2 : Quel est le niveau de maturité atteint par l'innovation ? Quelles sontles références industrielles ?
The GreenFlow heating system was developed and tested on furnaces at the Ipsen FutureLab.Several systems (the first one for 1.5 years) are currently in use at customer sites and are being used for production.Both systems with endogas or nitrogen/methanol heating are in use.
Question 3 : Expliquez comment l'innovation peut contribuer à la performanceindustrielle de son utilisateur. Sur quels critères peut-on mesurer son impact ?
The GreenFlow heating system enables users/customers to save up to 80% of the process media previously used (while maintaining the same quality of heat treatment results).This leads to more energy-efficient and therefore more cost-effective heat treatments, giving users a price advantage over their competitors. In addition to the above-mentioned reduction in resource consumption, CO2 emissions are also reduced, which significantly improves the CO2 footprint of the heat treatment process (again an advantage over the competition).
Question 4 : Expliquez le contenu technologique de l'innovation. Quels étaient les défis techniques à relever ? Quelles sont les solutions / technologies concurrentes ?
High-precision monitoring of the furnace atmosphere with the GreenFlow gas supply system makes it possible to use only as much process gas for heat treatment as is necessary to achieve the desired heat treatment results. (Previously, too much gas was always used to compensate for fluctuations/irregularities in the furnace atmosphere).
The biggest challenge was developing suitable (gas) analysers and control concepts to ensure a uniform furnace atmosphere (while complying with all safety requirements).As far as we know, there is currently no comparable market-ready competitor product, which makes the GreenFlow gas supply system a unique selling point for Ipsen.
To our knowledge, there is currently no comparable market-ready competitive product, which makes the GreenFlow gas supply system a unique selling point (USP) for Ipsen.The GreenFlow system is a unique solution for the specific requirements of Ipsen.
Question 5 : L'innovation contribue-t-elle à améliorer l'impact environnemental de l'utilisateur industriel ?
Yes, by drastically reducing the process media used (e.g. natural gas, methanol and nitrogen) as well as reducing the heating energy required (natural gas or electrical energy) and thus also drastically reducing CO2 emissions.
-
Depuis des décennies la profondeur de trempe est vérifiée par échantillonnage grâce à des contrôles destructifs qui sont longs et couteux : sciage, enrobage, polissage, filiation de dureté.
En implémentant une surcouche d'IA Deep Learning à sa technologie de contrôle par courants de Foucault multifréquences et multi-harmoniques, ibg permet de prédire de façon non destructive la profondeur de trempe sur pièce cylindrique avec une précision de +/-75 μm.
Question 1 : Dans quel(s) contexte(s) l'innovation est-elle envisagée ?
L'innovation s'intègre en aval des traitements thermique par induction en moyenne ou grande série. Elle peut être déployée au laboratoire métallurgique mais aussi en ligne automatisée pour un contrôle à 100%.
Question 2 : Quel est le niveau de maturité atteint par l'innovation ? Quelles sontles références industrielles ?
Une application industrielle est en fonctionnement depuis plus d'un an. 2 sont en cours d'implémentation.
Question 3 : Expliquez comment l'innovation peut contribuer à la performance industrielle de son utilisateur. Sur quels critères peut-on mesurer son impact ?
L'amélioration de la performance est triple.
1- amélioration de la qualité/sécurité par une meilleure détection des pièces non conformes
2- réduction des coûts de contrôle : pas de consommable avec les courants de Foucault, non destruction de pièces, réduction du temps de mains d'œuvre.
3- gain de temps : le contrôle est instantané (quelques secondes) et la production n'est plus obligée d'attendre les résultats du laboratoire pendant plusieurs dizaines de minutes.
Question 4 : Expliquez le contenu technologique de l'innovation. Quels étaient les défis techniques à relever ? Quelles sont les solutions / technologies concurrentes ?
Avant l'innovation, le contrôle par courants de Foucault d'ibg était très performant grâce à l'utilisation en simultané de 8 fréquences et de 2 niveaux d'harmoniques. Chaque composant était ainsi évalué par 24 couples de cordonnées X,Y dans le plan d'impédance.
Cela est largement suffisant pour détecter toute hétérogénéité métallurgique (différence de microstructure ou de composition chimique).
Le défi a relevé était d'arriver à traiter ces données pour prédire une profondeur de trempe exprimé en mm et non plus seulement une sanction bonne/mauvaise.
Nous avons compilé de très nombreuses données croisées en mesure de dureté (destructif) et en CF (non destructives). En parallèle, nous avons développé d'un modèle d'IA adapté basé sur du Deep Learning (Réseaux neuronaux convolutifs - CNN).
Le modèle ainsi développé est générique pour les composants cylindriques traités par induction. Il s'agit de fusées de joints homocinétique (CV joint), d'arbres de transmission, de tige de vérins...
Question 5 : L'innovation contribue-t-elle à améliorer l'impact environnemental de l'utilisateur industriel ?
Oui. En réduisant significativement le nombre de composants détruits pour analyse, l'impact environnemental de l'industriel est réduit.
Qui plus est, la meilleure maitrise de la profondeur de trempe par induction permet de réduire l'énergie électrique utilisée pour l'induction. Même si la réduction est modeste en %age, il s'agit d'un des postes de consommation les plus importants et les gains finaux sont substantiels.
Les Prix de thèse A3TS 2025
L’A3TS a organisé, cette année encore, un prix de thèse francophone afin d’encourager et mettre en avant des travaux de développement de savoirs technologiques de pointe en traitement thermique et en traitement de surface.
Les lauréats ont présenté leurs travaux sur le forum du salon et ont été invités aux Conférences. Nous leur adressons nos chaleureuses félicitations !
Concours photo A3TS 2025
🏆 Premier Prix
Concours Photo A3TS 2025 : les lauréats à l'honneur
Dans le cadre du congrès MATTRIS 2025, le concours photo A3TS s’est tenu sur le thème « Les traitements des matériaux sous l’œil du microscope ». Porté par une équipe d’organisation composée de membres de l’A3TS, de l’enseignement et de l’industrie, le concours a une nouvelle fois mis en avant la technicité, la créativité et le sens de la communication des participants.
Le jury, composé de représentants de l’A3TS, de LAM Plan, d’Oerlikon, de Bodycote et du monde académique, a attribué les prix suivants :
🏆 Premier Prix : Une nuit étoilée - Pauline Mougeot, UFR Sciences et Techniques - Besançon
🔧 Prix de la technicité : De la cémentite dans le granit ? - Jean Stemmelen, Lycée Jean Mermoz - Saint-Louis
🎨 Prix de l’originalité : Origami en metal argenté autour d'un lac - Théo BERTHUIT, Lycée Théophile Roussel - Saint-Chély d’Apcher
📢 Prix de la communication : Paysage post-volcanique et rivières de carbures - Chems-edine ZOUAIMIA, Lycée Jean Mermoz - Saint-Louis
Chaque prix a été récompensé par des bons d’achat en produits de préparation de laboratoire, offerts par l’A3TS et LAM Plan.
Félicitations à tous les lauréats ! Rendez-vous l’année prochaine à Dunkerque pour une nouvelle édition du concours !
Un grand merci à notre partenaire LAM PLAN pour son implication et sa contribution à cet évènement.


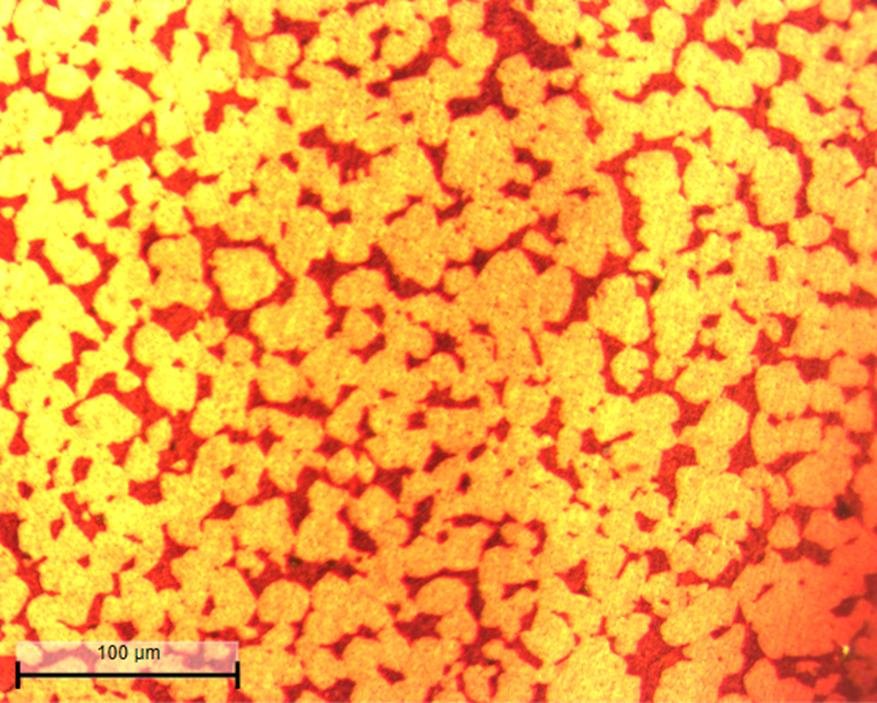
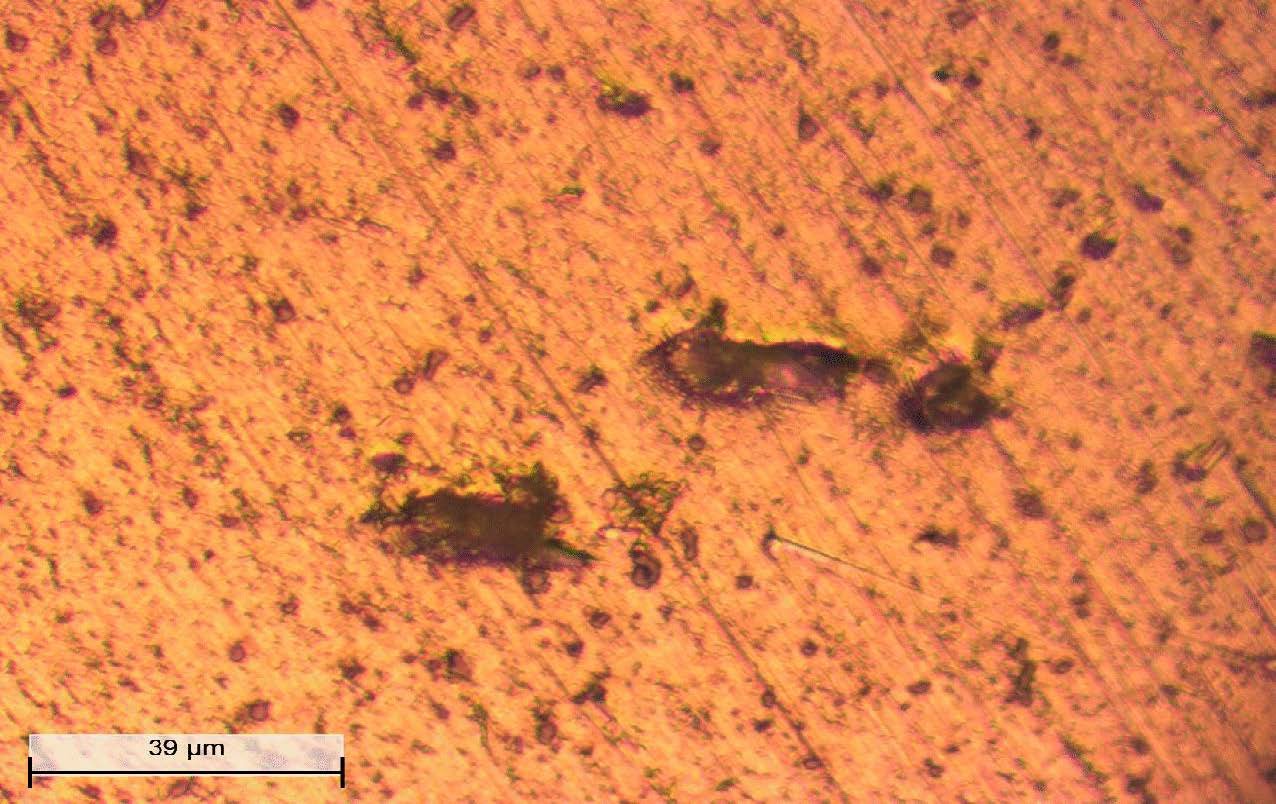
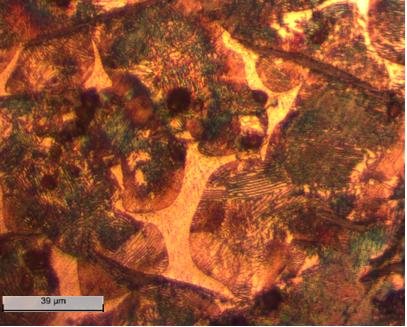


Les trophées Jeunes UITS 2025 :
Le 3 juillet a eu a remise des prix du concours des Trophées UITS Jeunes Étudiants 2025.
Cette année la thématique centrale était le secteur de l’Energie avec les différents procédés associés en traitements de surface et traitements thermiques.
Les participants devaient mettre en valeur la créativité, l’esprit d’équipe et d’innovation en faisant appel à l’ensemble des procédés de traitement des matériaux.
Bravo aux lauréats pour leur engagement et leurs superbes créations !
IUT Besançon-Vesoul – Gagnant du Prix de l’Innovation
IUT Besançon-Vesoul – Coup de cœur du jury
ENSIL-ENSCI (Limoges) – Gagnant du Prix de la Technicité
Master FTS – Formulation et Traitement des Surfaces (Besançon) – Gagnant du Prix de l’Esthétisme ET du 1er Prix de l’Édition 2025
📅 Rendez-vous en 2027 pour la prochaine édition des trophées UITS !
Job Dating
Le jeudi 3 juillet matin a eu lieu le job dating sur le salon. De nombreux candidats ont pu rencontrer les exposants présents.
Tous les acteurs et sociétés ont eu des rendez-vous avec des candidats de qualité permettant d’envisager des recrutements et potentiels collaborateurs.
Retrouvez toutes les offres d’emploi encore disponibles ici :
https://www.a3ts.org/offres-demploi
Soirée exceptionnelle au Château de Marsannay
Le 3 juillet dernier, la soirée de gala de MATTRIS '25 by A3TS a réuni 250 participants au cœur de la Bourgogne, au prestigieux Château de Marsannay, emblème de la Cité du vin et de la gastronomie.
Dans une atmosphère conviviale, les invités ont pu découvrir les vignes environnantes et déguster quatre grands vins du domaine.
Après un cocktail d’accueil et une déambulation dans les caves du château, le dîner s’est tenu dans une magnifique cave voûtée. La soirée a été ponctuée par l’intervention d’un magicien mentaliste, dont les tours bluffants ont émerveillé l’assemblée.